by Rohde Brothers | Mar 19, 2024 | HVAC, Service
As we step into 2024, the HVAC industry continues to evolve with technological advancements and a growing focus on efficiency and sustainability. Updates to state and municipal codes require increasingly efficient systems to protect the environment and the health of occupants. For engineers and facility managers, staying ahead means adapting to these changes and implementing state-of-the-art strategies to optimize HVAC system performance. This article dives into the latest techniques and technologies that are shaping the future of HVAC systems in commercial and industrial settings.
Advanced Control Systems: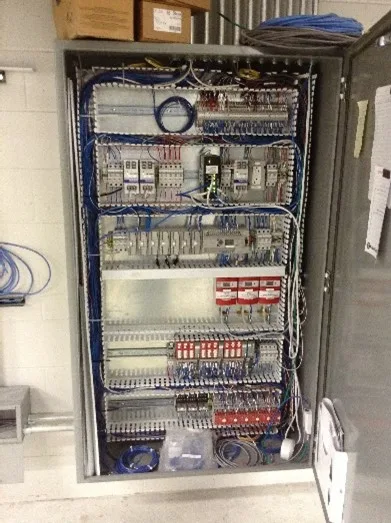
The heart of modern HVAC efficiency lies in advanced control systems. These systems employ real-time data analytics and machine learning algorithms to continuously monitor and adjust settings for optimal performance. For example, smart thermostats and Building Automation Systems (BAS) can now predict occupancy patterns, adjust temperatures based on real-time weather data, and identify areas to optimize. Occupancy sensors and carbon dioxide sensors enable the BAS to optimize for comfort and efficiency.
Variable Frequency Drives (VFDs):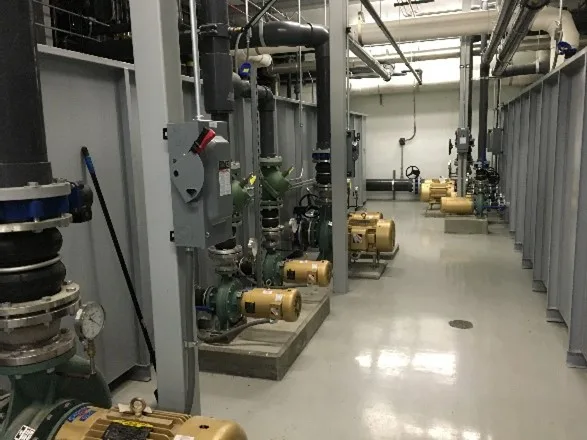
VFDs have become the standard in energy conservation. By controlling thespeed of motor-driven equipment based on demand, VFDs significantly reduce energy consumption. In 2024, the integration of VFDs with BAS for real-time adjustments based on occupancy and usage patterns is a game changer, offering potential energy savings of up to 30-40% in systems like air handlers, chillers, and water pumps.
High-Efficiency HVAC Equipment:
The shift towards high-efficiency HVAC equipment is more pronounced than ever. The international mechanical code and international energy code require energy efficiency improvements. The latest models of chillers, condensers, and heat pumps come with higher Seasonal Energy Efficiency Ratios (SEER), Energy Efficiency Ratios (EER), and Coefficient of Performance (COP) values. For instance, modern chillers incorporate magnetic bearing technology, permanent magnet motors, and variable speed compressors, reducing energy consumption and maintenance needs.
Indoor Air Quality (IAQ) Management:
IAQ has taken center stage, especially in the wake of global health concerns. Advanced HVAC systems now integrate IAQ sensors that monitor and control air quality parameters like CO2 levels, humidity, and airborne pollutants. Regular maintenance of air filters, ducts, and employing, ionization and UV-C light technology for air purification are key strategies in maintaining optimal IAQ.
Geothermal Heat Pump Systems: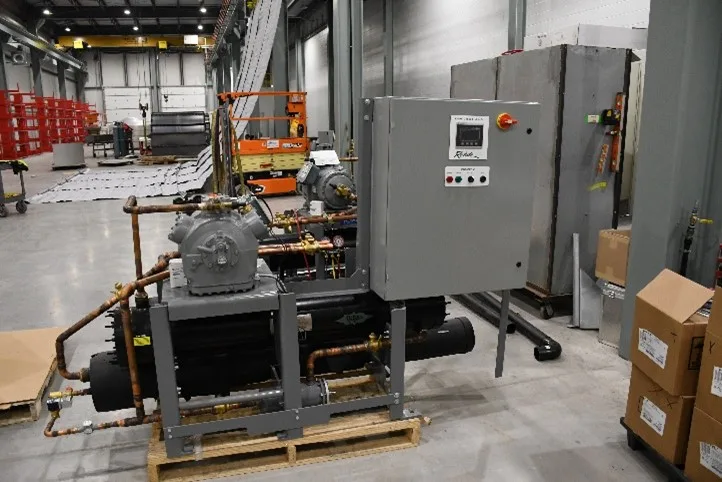
The use of geothermal heat pump systems is on the rise, leveraging the stable temperatures of the earth to provide heating and cooling. These systems offer significant energy savings and lower greenhouse gas emissions compared to traditional HVAC systems. The high upfront costs are typically more than offset by rebates, tax credits available through state and federal programs, and other incentives. This makes using these energy efficient systems much more attractive. Other green refrigerants are also considered regularly due to their unique advantages and cost savings.
Retrofitting and Upgrading:
For many facilities, completely overhauling the HVAC system is not feasible. Thus, retrofitting becomes a vital strategy. In 2024, consider retrofitting options such as adding Variable Frequency Drives (VFDs) and upgrading to smart thermostats or full building automation systems when it is time for replacements or upgrades. Replacing outdated components with high-efficiency alternatives provide a cost-effective way to enhance efficiency and air quality.
Conclusion:
The year 2024 presents exciting opportunities for optimizing HVAC systems in commercial and industrial environments. By embracing advanced control systems, VFDs, high-efficiency equipment, robust IAQ management, innovative geothermal solutions, and strategic retrofitting, engineers and maintenance directors can significantly improve system performance, reduce energy costs, and contribute to a more sustainable future. At Rohde Brothers, Inc., we are committed to providing innovative solutions and expertise to help you achieve these goals.
Choose Rohde Brothers, Inc. for HVAC Excellence
With Rohde Brothers, Inc., you’re choosing a partner committed to innovative, efficient, and sustainable HVAC solutions.
Contact us today to discuss how we can elevate your HVAC systems, reduce your energy footprint, and ensure optimal performance for years to come.
by Rohde Brothers | Jan 23, 2024 | Service
Choosing a commercial mechanical service partner is more than just another business decision; it is critical to the life of your building and your business. Why is it so critical? Mechanical systems are what make your facility functional and comfortable. For industries like food production, the importance of maintaining a temperature-controlled environment cannot be overstated. Mechanical systems in the food industry can be used in the production and packaging processes as well. Having a contractor doing your service regularly will provide a level of protection for your operations that will save you time and money overall.
Excellent Service is Critical to Your Operations
Do not underestimate the repercussions of making the wrong choice but focus on the positive and you will be just fine. Besides the obvious risk of being overcharged, there is also the potential for unreliable service and frequent equipment issues. On the other side, making an informed choice can provide you with a reliable partner who not only saves you time but also significantly reduces costs over the life of your equipment by implementing quality from day one. This is particularly crucial when you consider the operational setbacks like plant or process shutdowns, which can throw your production schedules into chaos.
Step 1: Comprehensive Research
Broaden Your Search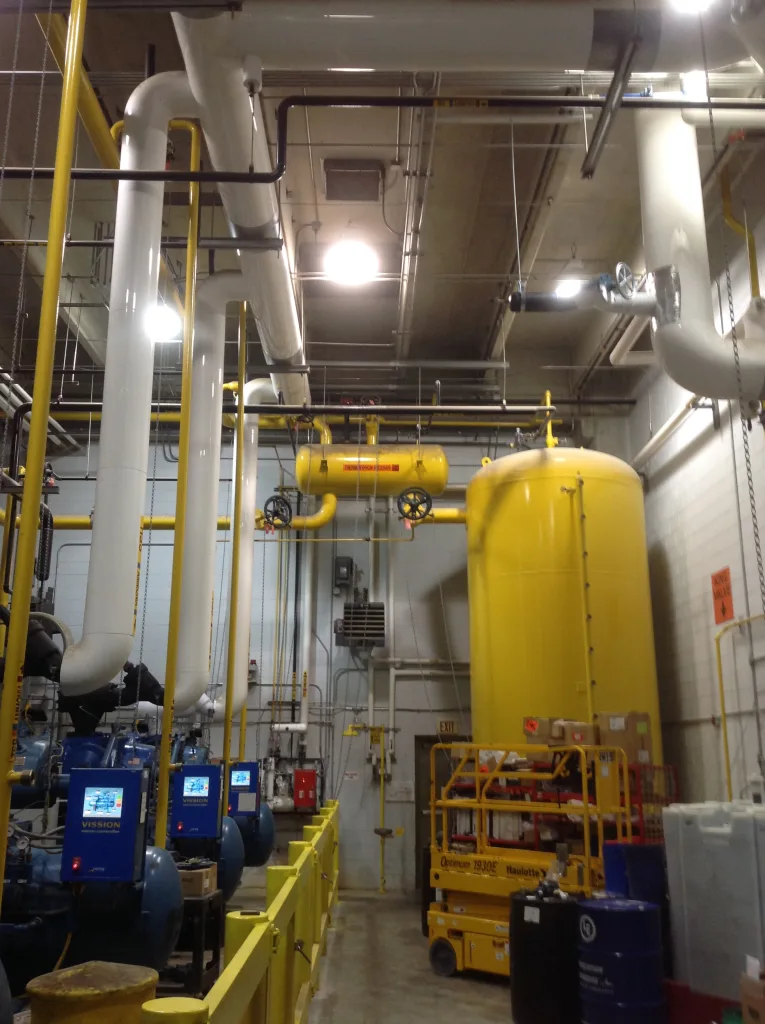
Start with a varied and wide-reaching approach. Do not rely solely on internet search results; while they are a good starting point, remember that SEO rankings do not necessarily correlate with service quality. If you are not new to the contracting business, you are probably already working on a list of firms that have done well by you and are trusted and reliable. If you are looking to add firms to your list, try some of these:
Industry-Specific Platforms: Websites designed for your industry can be goldmines of information, offering directories, reviews, and even case studies.
Business Directories: Platforms like Yellow pages and LinkedIn can offer a snapshot of potential contractors but be mindful that they often lack detailed evaluations.
Social Media and Online Forums: These platforms can provide real-life reviews and advice. Subreddits or Quora threads related to your industry can offer insider perspectives.
Trade Shows and Local Resources: Do not underestimate the power of face-to-face interactions. Your local Chamber of Commerce can be a fantastic resource, as can industry-specific trade shows.
Word-of-Mouth and Recommendations
Talk to your business network. Colleagues or industry contacts who have had firsthand experiences with contractors can offer invaluable insights.
Online Reviews for Additional Perspective
While they should be taken with a grain of salt, websites like Yelp and Google Reviews can give you a feel for customer satisfaction and company responsiveness.
Step 2: Verify Credentials Rigorously
Insist on Certifications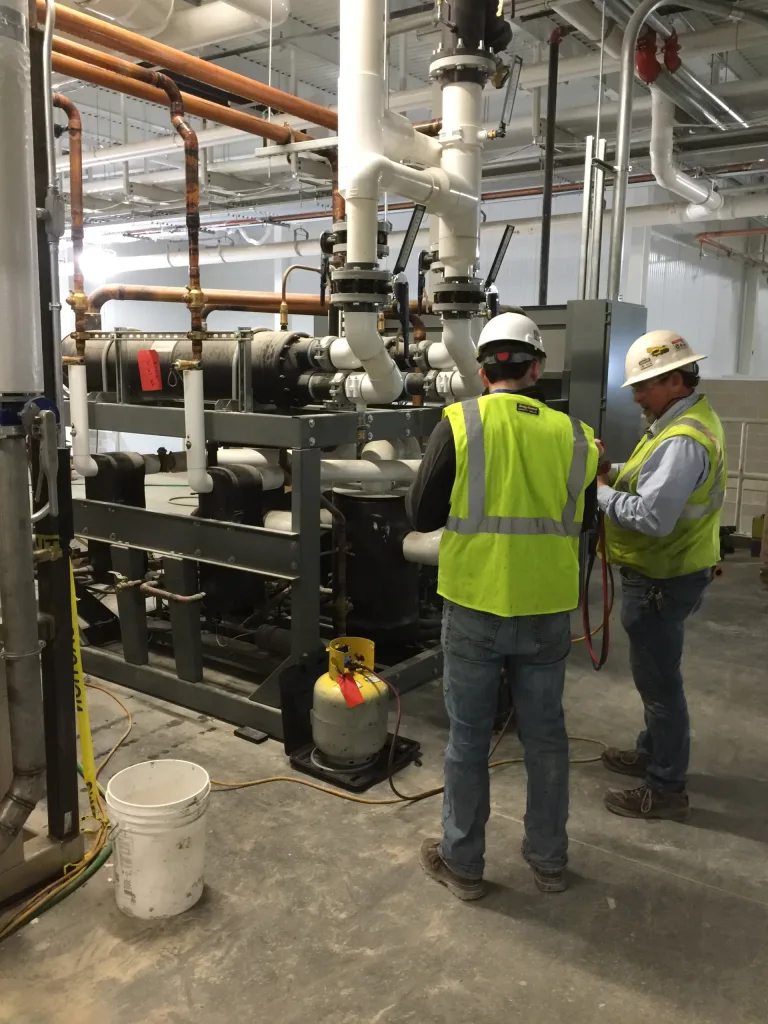
Reputable companies should willingly display their industry certifications, which validate their expertise and credibility.
The Weight of Experience
An established track record is often a good predictor of future performance. Companies that have been around have typically done so by delivering consistent, high-quality service.
Step 3: Obtain and Analyze Quotes
Detailed Proposals
Request a thorough breakdown that lists
not only the cost but also the scope of
work, materials needed, labor costs, and any other factors like travel or lodging for workers.
Examine Price Factors Carefully
Ensure you understand what is driving the costs in the quotes you receive. Do not just look for the cheapest option; seek value by understanding what each line item represents.
Step 4: Evaluate Customer Service and Flexibility
Initial Interactions Matter
How a company engages with you at the beginning often sets the tone for your entire relationship. Do they respond in a timely, professional manner? Are they transparent about their capabilities and limitations? Being comfortable with your interactions is a key part of building a great relationship.
Be Mindful of Availability
Emergencies do not wait. Ensure your prospective service partner has the bandwidth and resources to assist you when unplanned issues arise. The best service partners are available when issues arise period, if your service partner makes you wait for emergency service, you can do better.
Step 5: Read the Fine Print
Understand Your Contract
Contracts safeguard both parties. A reputable company will encourage you to read the contract carefully and will gladly clarify any ambiguities.
Wrapping It Up
Navigating the complexities of selecting a commercial mechanical service provider does not have to be a minefield. With a little due diligence, you can find a partner who brings more than just technical skills and talented technicians to the table; they bring peace of mind.
About Rohde Brothers, Inc.
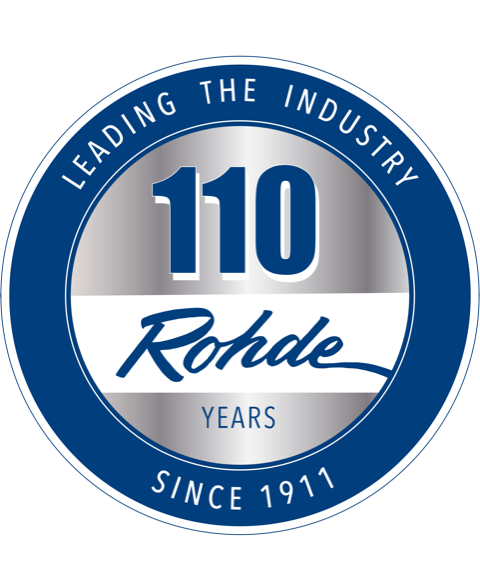
With more than 110 years in the business, our commitment to quality and customer satisfaction is unparalleled. Our technicians are not just skilled; they are experts in the field. They have built some of the most complex mechanical systems in the world, right here in Wisconsin. Our techs are embedded in some of the largest manufacturing facilities, and we also serve some of the smallest. Our in-house fabrication, engineering, and construction teams are ready to go to work for you.
Final Thoughts
Remember, choosing the right mechanical service provider is more than just a business decision; it is an investment in the smooth operation and success of your facility.
Contact Rohde Brothers, Inc. to take the first step toward a partnership that prioritizes your peace of mind and operational excellence. Mike Kruschke is the Service Manager at Rohde Brothers, Inc. and has decades of experience in servicing mechanical infrastructure and equipment. Click the Email Button Below to let us know how we can help.
Call for Service: 920-893-5905
by Rohde Brothers | Dec 15, 2023 | Service
As plant managers, maintenance experts, and engineering professionals, we know the backbone of any operation involving temperature-sensitive goods is its refrigeration system. It’s not just about getting and keeping products cold; it’s about efficiency, and reliability. Regular maintenance can account for 12 to 18% return annually in the form of energy savings. Not only that, according to Doug Biedenweg, an industrial process engineer, for every $1 dollar in maintenance deferred you will pay $4 in capital renewal costs when that equipment fails. That seems to make sense right? If so, don’t defer the critical maintenance that will make those savings reality.
Optimizing Operational Efficiency
In any industrial setting, operational efficiency is the cornerstone of performance and profitability.
A well-maintained refrigeration system is synonymous with optimized operational efficiency. For example, keeping coils clean and belts properly tensioned can ensure that heat transfer is always optimized. When heat transfer isn’t optimized, equipment runs longer, resulting in the use of more energy for the same amount of work. And we all know what that means: higher operational costs to the tune of 12 to 18%, and a reduced bottom line. Preventative maintenance ensures that every component is optimized, thus minimizing energy draw and the resulting operating costs.
Friction is the enemy of energy efficiency, most people agree on that, but so many times we see equipment that isn’t lubricated properly, and the compressors or fans have failed in a way that could have been avoided.
Maximizing Equipment Lifespan
From an asset management perspective, the longevity of your refrigeration system is paramount. Regular maintenance is not just about preventing breakdowns; it’s about extending the life expectancy of your equipment. When you inspect your equipment regularly you can monitor and remove debris which may be hiding an issue. Each maintenance session is an opportunity to catch early signs of wear and to replace parts before they fail. This is essential for planning capital expenditures and avoiding the financial burden of a plant shutdown. According to statistics, using critical equipment to failure costs as much as 10 times more than the maintenance program that would have prevented it. The larger the operation, the more expensive downtime becomes, in some cases costing hundreds of thousands to perhaps a million dollars per hour.
Guaranteeing Product Integrity
Product quality is non-negotiable, and a lapse in refrigeration can be catastrophic. Downtime in a cheese storage facility, for example, can be catastrophic. You spend money on the latest control systems that keep your temperatures optimal 24/7, however, downtime due to lack of maintenance can render those controls useless. Product recalls will result in lost revenue and could easily damage your reputation. Maintaining a constant temperature can be critical to your product’s flavor development, ageing, and freshness.
Minimizing Downtime Risks
Downtime is a threat to productivity and profitability. An unexpected failure can halt production lines, lead to inventory losses, and spoilage which can affect delivery schedules. Regular maintenance helps to prevent these scenarios by ensuring that potential issues are addressed before they lead to system failure.
If you’re inspecting your equipment and fixing repairs, you may be able to go for very long periods of time with no downtime. Time is money.
Prioritizing Workplace Safety
In the world of industrial refrigeration, a system failure isn’t just an operational issue—it’s a safety concern. While ammonia is typically safer than halocarbon-based refrigerants, leaks of refrigerants, such as ammonia, or halocarbons, can be hazardous. For example, ASHRAE has a classification system, and that’s an article that we don’t have the time for in this article. ASHRAE provides that a letter and number are issued to refrigerants based on their toxicity and flammability. Understanding that halocarbons are typically more flammable and with propane, ethylene, and butane in their names you quickly make the connection. The big thing to remember is maintenance is critical for the safety of the plant personnel regardless of the type of refrigerant. It’s our duty to maintain a safe working environment, and regular system inspections are a cornerstone of this commitment.
Facilitating Financial Forecasting
Effective maintenance regimes allow for predictable financial forecasting. By having a maintenance schedule, you can plan for the associated costs in your operational budget. This forward planning reduces the risk of financial surprises associated with emergency repairs and system downtime.
Predictive or preventative? Once you understand the optimal maintenance patterns for your equipment you can look at predictive maintenance as an added layer of financial forecasting and potential savings. Predictive maintenance on industrial refrigeration systems can save as much as 40% in terms of costs over reactive, and 8-12% over preventative maintenance. Why? Because adding maintenance when your equipment needs it most is optimization in the most fundamental sense.
In conclusion, the message is clear: ignoring industrial refrigeration maintenance is a risk you cannot afford. It is your responsibility to ensure that your refrigeration systems are not just functioning but are performing efficiently, safely, and in compliance with all regulations. So, it pays to prioritize maintenance, not just as a routine task, but as a strategic imperative for the success of your operations.
Keep the gears turning, the products chilled, and the operations flowing.
Rohde Brothers, Inc. has experience in designing, installing, controlling, and maintaining industrial refrigeration systems. To schedule a maintenance inspection, reach out to Service Manager, Mike Kruschke at 920-893-5905 today!