Boost Efficiency, Prevent Downtime, and Save Money
As winter approaches, facility managers and maintenance teams face unique challenges in keeping industrial mechanical systems running smoothly and efficiently. Cold temperatures can lead to increased wear, higher energy consumption, and unexpected downtime. But with a proactive winter maintenance plan, you can protect your mechanical assets, optimize performance, and reduce operating costs. In this guide, we cover the most critical maintenance tasks for winter, helping your facility remain productive, efficient, and resilient all season long.
Service and Calibrate HVAC Systems for Optimal Efficiency
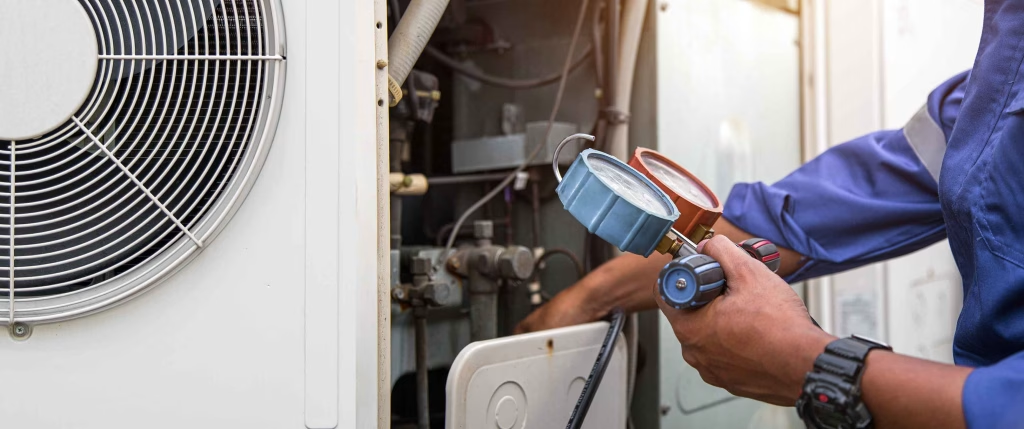
Key Points: Heating systems, filters, controls, and ventilation.
- Inspect Heating Systems: Boilers, furnaces, and other heating equipment should be professionally inspected, cleaned, and calibrated for winter use. Well maintained and tuned burners operate at peak efficiency and minimizes energy waste.
- Replace Air Filters: Dirty or clogged filters restrict airflow, forcing HVAC systems to work harder. Replacing filters reduces strain on equipment, saves energy, and keeps indoor air quality high.
- Check Ventilation: Proper ventilation is crucial in winter. Too little airflow causes poor air quality. Too much outside airflow wastes energy. Inspect and clear any blockages in ventilation ducts to ensure a continuous flow of fresh air and reduce strain on HVAC systems. Confirm dampers are working properly.
Savings Insight: Efficient HVAC systems can reduce energy bills more than 20% during winter, a significant savings in an industrial setting.
Prepare and Protect Pipes to Prevent Freezing
Key Points: Insulation, heat tracing, and water temperature.
- Insulate Exposed Pipes: Insulation helps maintain pipe temperatures, reducing the risk of freezing and subsequent damage as well as minimizing energy loss.
- Use Heat Tracing for Critical Pipes: Heat tracing cables provide direct heat to pipes, which is especially beneficial for critical process piping. Ensure the system is operational and calibrated to activate during low temperatures. Focus on pipes in unheated areas or those located near exterior walls.
- Monitor Water Temperatures: Cold weather can affect water temperatures, impacting certain processes. Consistently monitor and adjust to maintain safe temperatures that won’t stress pipes or equipment.
Savings Insight: Proactive pipe maintenance helps prevent costly repairs, downtime, and potential damage to the facility due to burst pipes.
Perform Routine Maintenance on Pumps and Motors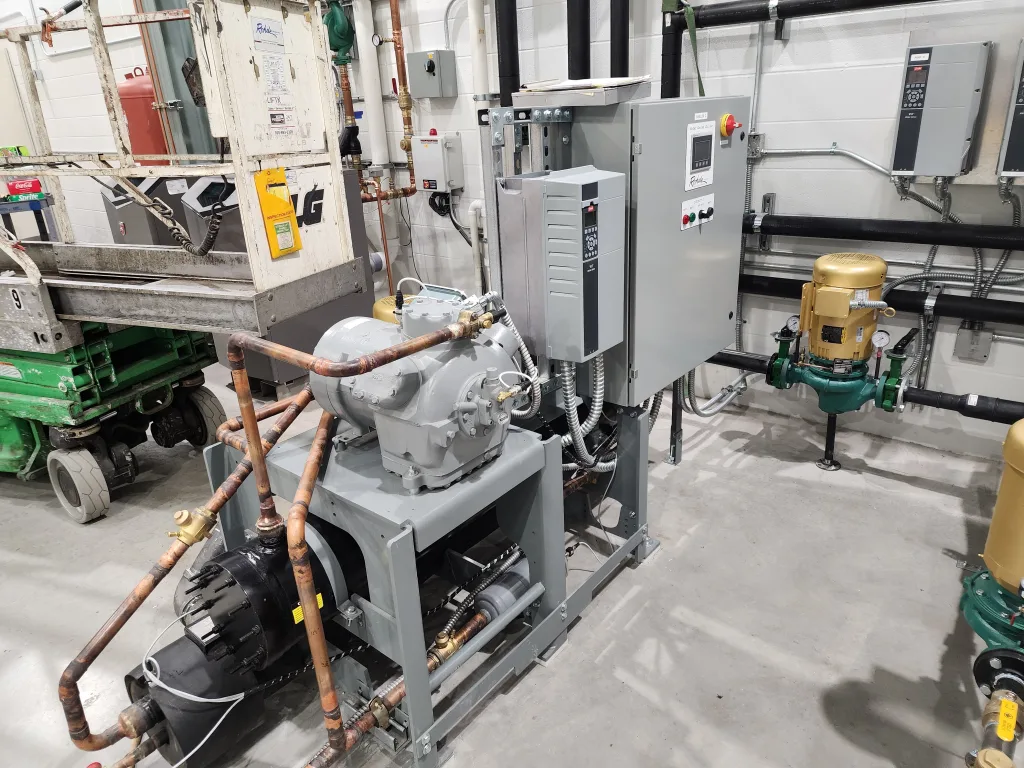
Key Points: Lubrication, seals, and vibration analysis.
- Lubricate Moving Parts: Cold weather can cause lubricants to thicken, leading to additional wear on pumps and motors. Regularly lubricate moving parts to reduce friction and ensure smooth operation. Be careful not to over-lubricate, which can cause increased friction and reduced efficiency.
- Inspect and Replace Seals: Cold weather can harden seals, leading to leaks or pressure drops. Inspect seals on all pumps and motors and replace any showing signs of wear.
- Conduct Vibration Analysis: Excessive vibration can be a sign of imbalance or misalignment in pumps and motors. Regular vibration analysis helps identify potential issues early, reducing the risk of breakdowns.
Savings Insight: Properly maintained pumps and motors consume less energy and have a longer lifespan, reducing the need for costly replacements.
Maintain Water and Wastewater Treatment Systems
Key Points: Tank heaters, drain lines, and pump inspections.
- Install or Test Tank Heaters: Cold temperatures can cause water in outdoor tanks to freeze, disrupting processes. Ensure tank heaters are installed and functioning properly to maintain consistent temperatures.
- Inspect and Clear Drain Lines: Blocked drains can freeze over in winter, leading to backups or overflows. Regularly clear drain lines to prevent ice buildup and ensure smooth water flow.
- Pump Inspections: Winter can be tough on pump systems due to cold, thickened fluids. Inspect pumps for signs of wear and verify that they can handle increased resistance from colder, thicker fluids.
Savings Insight: Preventing freeze-related issues in water systems helps avoid unexpected downtime and maintains process integrity.
Inspect and Test Backup Power Systems
Key Points: Generators, fuel levels, and load testing.
- Generator Inspections: Power outages are more common in winter, so it’s essential to ensure that backup generators are ready to handle unexpected demand. Conduct a full inspection, checking fuel levels, battery health, and connections.
- Perform Load Testing: Load testing helps verify that your backup system can handle the facility’s power needs during an outage. Schedule these tests regularly to avoid unpleasant surprises.
- Check Fuel Quality and Storage: Cold weather can cause diesel fuel to gel. Make sure fuel tanks are properly maintained and consider using winter-grade fuel or additives to prevent gelling.
Savings Insight: Reliable backup power prevents costly downtime, safeguarding your operations even during winter storms.
Implement Energy Management and Monitoring Systems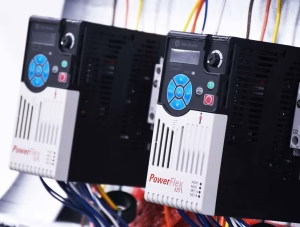
Key Points: Smart controls, energy monitoring, and data analysis.
- Smart Control Systems: Consider installing or updating control systems to automate temperature adjustments and regulate energy use based on facility needs.
- Continuous Energy Monitoring: Monitoring energy usage across heating, ventilation, and process systems gives facility managers insight into where energy use spikes, allowing for targeted efficiency improvements.
- Data Analysis for Efficiency Gains: Reviewing data from energy management systems can reveal areas for improvement, such as adjusting heating levels or scheduling system downtimes.
Savings Insight: Energy management systems provide actionable insights, allowing you to reduce unnecessary energy expenses and optimize equipment performance.
Final Thoughts: Plan Proactively to Save Big This Winter
Winterizing industrial mechanical systems isn’t just about getting through the season—it’s about running a safer, more efficient, and cost-effective operation all winter long. By implementing these maintenance steps, facility managers can reduce the risk of unexpected downtime, protect valuable equipment, and significantly reduce energy costs.
Ready to keep your facility winter-ready and efficient? Let’s build something together.
Winter is coming, and your industrial mechanical systems need to be ready. Don’t let freezing temperatures cause costly downtime, skyrocketing energy bills, or unexpected repairs.
Download our Essential Winter Maintenance for Industrial Mechanicals Checklist to:
✔ Boost HVAC efficiency and cut energy costs by up to 20%
✔ Prevent pipe freezes and protect critical infrastructure
✔ Extend the lifespan of pumps, motors, and other essential systems
✔ Ensure backup power is ready for winter storms
Equip your team with a proven step-by-step guide to keep your facility running smoothly, efficiently, and safely all winter long. Just fill the form out and we’ll send the checklist directly to your inbox.