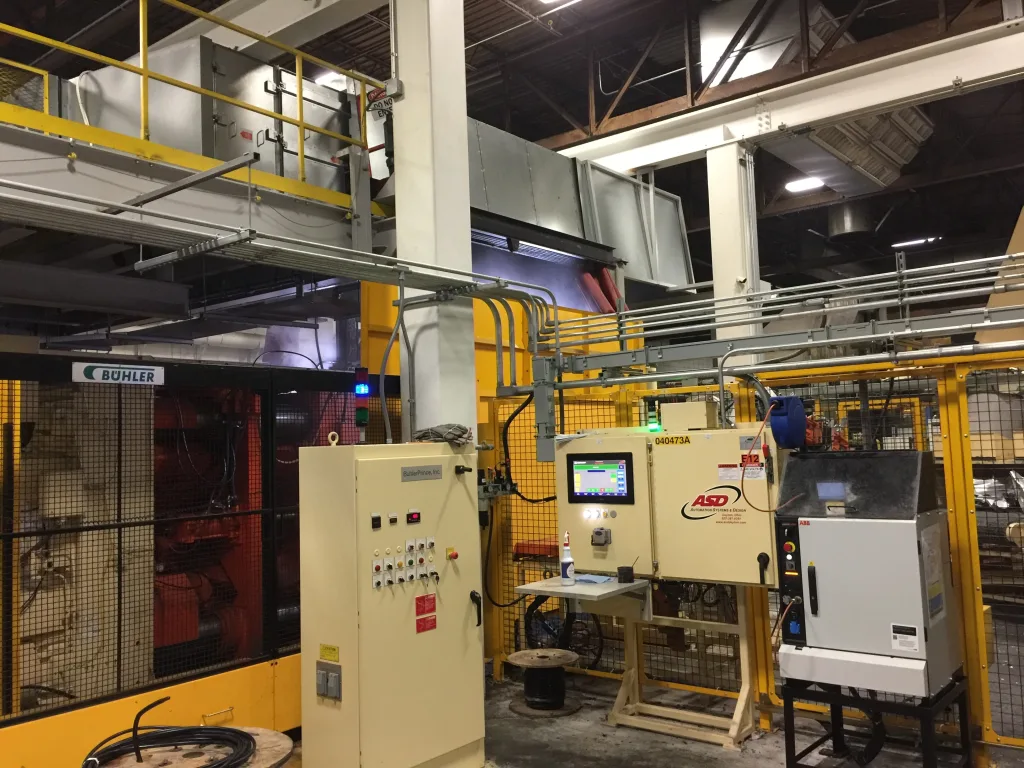
The Challenge: Mercury Marine faced a challenge with their expansion, including the addition of three new die cast machines. They needed an advanced air filtration system to handle the increased output and maintain a clean, safe work environment.
Our Solution: We developed a tailor-made air filtration system featuring:
- Retractable Hoods: These allow easy die changes without compromising air quality.
- Advanced Four-Stage Filtration: This system efficiently removes contaminants, recirculating clean air back into the facility.
- Customizable Fan Speeds: Variable speed fans for each machine provide precise control over air flow.
- Integrated Control System: A custom PLC, integrated with Mercury’s central system, offers seamless operation and monitoring.
Adapting to Expansion: When Plant 17 added a larger, 4500 ton capacity machine, we modified our system to match. This included redesigning the hood and piping systems and integrating new heating and cooling equipment for better efficiency.
Results and Impact: Our initial success led to the installation of ten mist collection systems across the facility, significantly improving air quality and operational efficiency.
Conclusion: This project with Mercury Marine is a prime example of Rohde Brothers’ commitment to innovative and efficient industrial solutions. If you’re looking for a partner to enhance your facility’s performance and safety, we’re here to help.
Rohde Brothers Inc. – Lets Build Something Together